Chemical Safety
What is Chemical Safety?
Chemical safety is the practice of handling chemicals in a safe manner by minimizing the hazard to personal health and the campus community. Chemical safety has many scientific and technical components. Among these are ecotoxicology, toxicology, and the process of chemical risk assessment which requires a detailed knowledge of exposure and biological effects.
Chemical safety is achieved by assuming the responsibility of all activities involving chemicals in such a way as to ensure the safety of human health and the environment. It covers all chemicals, natural and manufactured, and the full range of exposure situations from the natural presence of chemicals in the environment to their extraction or synthesis, transport use, and disposal.
The goal of the chemical safety program is to provide an environment for employees and students that is free from potential exposure to the chemicals that are used in the university. This program provides information and guidelines to address the proper use, handling, and storage of chemicals, which are mandated by federal, state, and local regulations. This program encompasses the chemical hygiene program for laboratories, and the hazard communication program for non-laboratory settings.
Please ensure that you refer to the chemical SDS sheets, receive proper training, and notify your Lab Manager prior to use of any chemical. Be prepared in case of an emergency or spill.
Broken Glass Containers in Laboratories
Broken glass containers, dustpan, and brush are available in all laboratories using glassware. Glassware must not be disposed of with normal trash. If your broken glass container is full or you need a replacement, please notify your Stockroom Technician for your area.
Laboratory broken glass containers must never be used for the disposal of:
-
Sharps
-
Biohazardous materials
-
Liquid wastes
-
Chemically contaminated laboratory glassware/plastics or plastic-ware
-
Chemical containers that cannot be disposed of as regular solid waste
Additional Criteria for Broken Glass Containers
It is important to reduce the risk of exposure when cleaning up broken glassware. Below is additional information regarding broken glassware and the use of broken glass containers.
Discarded glassware must adhere to the following criteria:
-
Broken glassware MUST NOT have any hazardous waste, medical waste, pathological waste, or radiological waste.
-
If your glassware has any of the specified wastes, please submit an EH&S Service Request and an EH&S specialist will be happy to assist you.
Broken glass containers must adhere to the following criteria:
-
Discarded glassware must be placed in a small puncture-proof, double-lined cardboard box or a container specifically designed for the disposal of glassware
-
Nothing other than broken glass should be in the container (i.e., gloves, wipes, trash)
-
No glass protruding from the container
-
The container must be labeled as to the contents
- Example: CAUTION! BROKEN LABORATORY GLASSWARE ONLY! NO HAZARDOUS WASTE, MEDICAL WASTE, PATHOLOGICAL WASTE, OR RADIOACTIVE WASTE
How to Clean up Broken Glass
Broken glassware should immediately be cleaned up to prevent further injuries from occurring. Below is a guidance for picking up and disposing of broken glass. If you are uncomfortable or require additional assistance reach out to your Stockroom Technician for help. Knowing what to do in the event of glassware breakage can help minimize injuries from occurring.
- Notify anyone working in the immediate area
- Prevent anyone from entering the area until the glass has been disposed of
- Protect yourself by wearing personal protective equipment (goggles, gloves, etc.)
- Dispose of the large pieces of glass first
- Sweep up any smaller pieces and dispose into the broken glass container
- Using a damp paper towel pick up any remaining shards
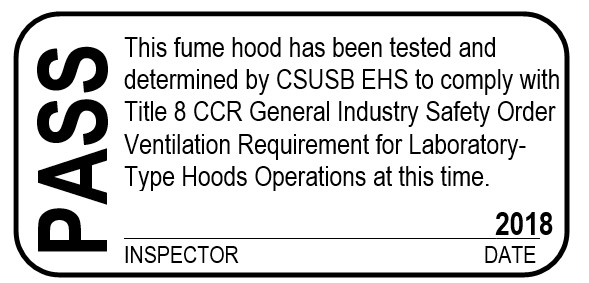
Chemical Fume Hoods
Chemical fume hoods are an important part of chemical safety. To better protect yourself and other lab workers, a proper chemical fume hood is required. Below are a few steps to ensure your fume hood is working as it should and help keep other lab workers safe:
- DO NOT use the chemical fume hood for storage. This prevents proper airflow when working with potentially hazardous chemicals. Remove unnecessary clutter, unused equipment, and apparatuses when not in use.
- CLOSE the chemical fume hood sash when work has concluded. This ensures that the chemical fume hood has a continued controlled airflow and prevents fumes from escaping into the ambient air should a malfunction occur.
- CLEAN UP any spilled chemicals and closed chemical containers in the chemical fume hood before concluding work. Chemical residues left uncleaned can cause potential hazards to others using the chemical fume hood and, depending on the type of chemical, can also cause degradation over time.
- BE VIGILANT about defects or potential malfunctions (this includes alarming fume hoods). If the issue persists, please submit a Work Order Request from Facilities Planning and Management to have a technician inspect the equipment
Fume Hood Certification
Environmental Health and Safety (EH&S) certifies all campus fume hoods annually using a calibrated anemometer and established protocols to ensure the face velocity is above the minimum values established by Cal-OSHA. The exhaust system needs to have an average face velocity of at least 100 feet per minute (fpm) with a minimum of 70 fpm at any point within the fume hood.
If EH&S cannot provide this service, EH&S will contract out to a certified vendor who will ensure all standards are met and applied. Users can see the label on the fume hood which indicates when the fume hood was certified and what the average face velocity is. The image below is an example of the "pass" label displayed on the fume hood.
Alarming Fume Hood
Fume hoods are often equipped with an audible/visual (A/V) indicator to indicate if the hood is not functioning properly. These A/V indicators alert laboratory personnel if there is insufficient airflow in the fume hood or laboratory ventilation equipment. When a fume hood is alarming, the fume hood is operating outside the approved parameters and does not meet regulatory requirements.
If the alarm on a fume hood is sounding:
- CONTACT Facilities Planning and Management Services at ext. 75175
- Give the location of the alarming fume hood and any additional information that could resolve the issue.
- CLEAR any chemicals in the fume hood and wipe the area down with solvent or soap and water to ensure no chemical residues are present and ready for when the technician arrives for service.
- DO NOT work and/or use fume hood until it has been cleared by the technician as mechanically functioning properly and re-certified by EH&S.
General Service of Fume Hoods
If the fume hood needs general service (e.g. change the light, etc.):
- SUBMIT a Work Order Request from Facilities Planning and Management to have a technician inspect the unit.
- Give the physical location of the fume hood and which fume hood needs service (if there is more than one in the laboratory area)
- Include what type of service is required and any additional information that may be useful for the technician. Remember the technician is not a scientist, so explaining how to maneuver in the laboratory may be useful.
- Carbon Copy (cc) EH&S (ehs@csusb.edu) before submitting Work Order, so that we know when service is completed, and EH&S can re-certify the fume hood.
- CLEAR any chemicals in the fume hood and wipe the area down with solvent or soap and water to ensure no chemical residues are present and ready for when the technician arrives for service
- DO NOT work and/or use fume hood until it has been cleared by the technician as mechanically functioning properly and re-certified by EH&S.
Informational Laboratory Safety Documents
Below are some informational safety documents on chemical safety. If you require specialized posters or consultation please submit an EH&S Service Request and an EH&S specialist will get back to you.
Documents
Laboratory Safety Procedures and/or Compliance (these documents are currently under review)
- Chemical Inventory and Reconciliation Procedure
- Procedure for Chemical Inventory
- Annual Inspections and Self-Inspections
Personal Protective Equipment (PPE)
Faculty and staff working in campus laboratories can find information in the Personal Protective Equipment (PPE) in the hazard assessment for your area in Risk and Safety Solutions (RSS) software and by referencing the Safety Data Sheets provided by the chemical manufacturer. If you would like additional information on the type of PPE that would work best with your laboratory functions, please request a consultation with one of our EH&S Specialists